Ausdrehkopf
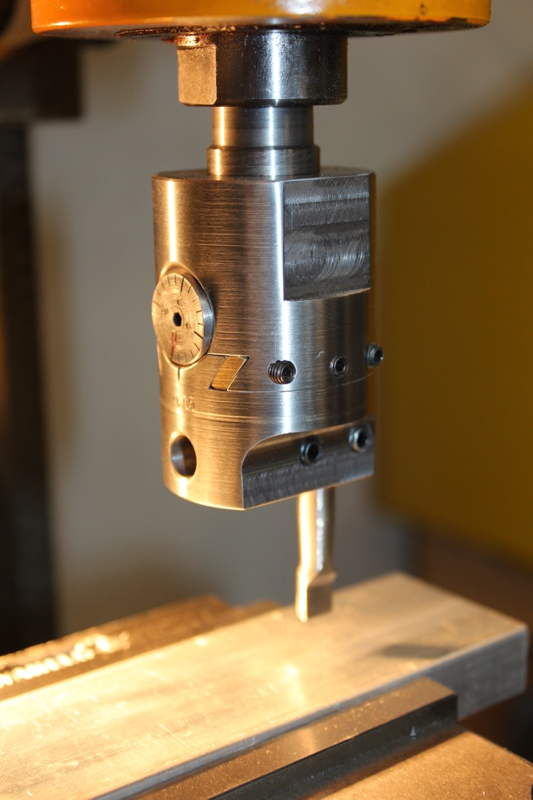
Dies ist ein Bauvorschlag für einen Ausdrehkopf zur Verwendung an der Fräse oder auch im Reitstock der Drehbank.
Ein Ausdrehkopf erlaubt das präzise Zustellen eines Ausdrehstahls zur Erzeugung von Bohrungen, für die entweder kein Standard Bohrer verfügbar ist, deren Größe über das Maß von handelsüblichen Bohrern hinausgeht oder deren Anforderungen an die Maßhaltigkeit über die Möglichkeiten von normalen Bohrern hinausgehen.
Der Ausdrehkopf ist dazu zweigeteilt: Er besteht aus dem Grundkörper, der mit einem Morsekegel (hier MK2) in die Spindel der Fräse aufgenommen wird und einem über eine Schwalbenschwanzführung horizontal verschiebbaren Oberteil, der einen Ausdrehstahl aufnimmt. Die Verschiebung und damit das Einstellen des Radius der zu erstellenden Bohrung erfolgt über eine Gewindespindel mit Skala. In diesem Bauvorschlag führt eine Drehung um einen Teilstrich zu einer Vergrößerung des Radius um 50um. Das Oberteil mit dem Werkzeug lässt sich über Schrauben am Grundkörper festklemmen.
Hinweise zum Bau
Der Ausdrehkopf besteht überwiegend aus gewöhnlichem Baustahl (ST52/S355). Die Druckleiste für die Schwalbenschwanzführung wurde aus Messing gefertigt.- Aufnahme: Für die Aufnahme in die Spindel der Fräse wurde ein MK2
Konus mit M10 Anzugsgewinde gefertigt. Werkzeugseitig erfolgt die
Verbindung zum Grundkörper des Ausdrehkopfes mit einem Feingewinde
M14x1 und einem Flansch mit 20mmm Durchmesser. Im Prototypen hat sich
gezeigt, dass die Zentrierung für diesen Anwendungsfall vollkommen
ausreichend ist. Durch die Verwendung des M14x1 Gewindes lassen sich
zudem später problemlos alternative Aufnahmen (andere Morsekegel, ggf. zylindrische
Aufnehmer) fertigen um den Ausdrehkopf an anderen Maschinen verwenden
zu können.
- Grundkörper: Der ST52-Abschnitt wird zunächst auf beiden Seiten
plangedreht und anschließend die M14 Gewindeaufnahme angefertigt. Auf
der Fräse werden dann zwei parallele Referenzflächen angebracht. Diese
sind wichtig, um beim späteren Weiterbearbeiten eine Parallelität der
Spindelbohrung zu den Schwalbenschwänzen zu ermöglichen. Zurück auf der
Drehbank wird dann die (Quer-)Bohrung für die Spindel eingebracht,
dabei ist ein präzises Ausrichten anhand der Referenzflächen mit einem
Fühlhebelmessgerät erforderlich. Das lässt sich gut im 4-Backenfutter
erledigen. An dieser Stelle wird auch das M6 Gewinde für die Spindel
geschnitten.
Nach nochmaligem Umspannen auf der Fräse werden schließlich die Schwalbenschwänze erstellt. Dazu wird zunächst der mittlere Bereich mit einem Zylinderfräser ausgefräst und schließlich die Schwalbenschwänze mit einem entsprechenden 60 Grad Fräser herausgearbeitet. Das Anfertigen der M4 Gewinde für die Klemmung erfolgt konventionell mit dem Handgewindebohrer.
- Oberteil: Analog zum Grundkörper wird dieser zunächst auf beiden
Seiten
plangedreht. Auf der Fräse wird dann der obere Teil mit Zylinderfäser
und Radiusfräser herausgearbeitet, dazu wird der zylindrische Rohling
senkrecht in den Frässchraubstock eingespannt. Dabei entstehen zugleich
Referenzflächen für die Weiterbearbeitung nach dem Umspannen.
Nach dem Umspannen (Unterseite nach oben) und päziser Ausrichtung mit Messuhr werden die Schwalbenschwänze gefräst - auch hier zunächst die Seiten mit einem Zylinderfräser und dann die eigentlichen Schwalbenschwänze. Dazu sollte der fertige Grundkörper kurz vor Erreichen der Sollmaße regelmäßig als Referenz herangezogen werden.
In dieser Aufspannung lässt sich dann auch gleich die innere Nut für die Spindel ausfräsen.
Nach dem Umspannen (Oberseite oben) - hierbei helfen zwei Stücke 6mm Silberstahl, eingelegt in die Schwalbenschwänze - werden die Werkzeugaufnahmen hergestellt. Vorbohren mit 7,8mm und Reiben mit 8mm H7 Reibahle. Nach weiterem Umspannen erfolgt analog die Bohrung für die seitliche Werkzeugaufnahme und das Ausarbeiten der äußeren Aussparung für die Spindel. Nach dem Anfertigen der Gewinde für die Werkzeugklemmung ist das Oberteil damit fertiggestellt.
- Spindel: Die Spindel wird in einer Aufspannung gemäß Zeichnung
gedreht.
Zum Verstellen der Spindel wird eine M5 Madenschraibe verwendet, die
mit Sekundenkleber in die zugehörige Gewindeaufnahme eingeklebt und
anschließend nochmals abgedreht wird.
Im Prototyp wurde als Skala eine 20er Teilung vorgesehen. Das ergibt bei der verwendeten M6x1 Spindel eine Verschiebung pro Skalenstrich um 50um. Die Skala selber wurde mit einem im Oberschlitten eingespannten HSS Werkzeug und dem Quersupport gestoßen, die Ziffern anschließend von Hand mit Schlagbuchstaben 2mm eingebracht. Ein wenig Farbe in den Ziffern und Skalenstrichen hilft den Kontrast zu verbessern.
- Finish: Die drei Teile Grundkörper, Oberteil und MK2 Konus werden miteinander verbunden und das Oberteil mit den Madenschrauben geklemmt. Die Spindel wird in diesem Zuge nicht montiert. Nach Aufnahme in die Drehbank kann nun der gesamte Ausdrehkopf außen abgedreht und den eigenen Ansprüchen gerecht geschliffen werden. Anschließend erfolgt ein manuelles Entgraten sämtlicher Kanten und Zusammenbau. -Fertig.
Bilder:
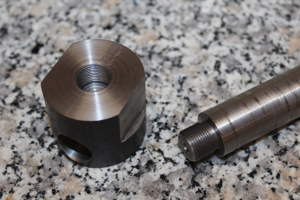
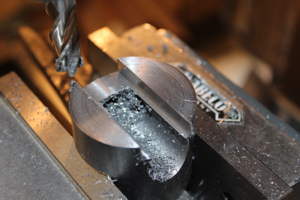
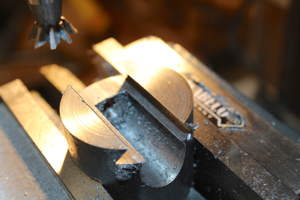
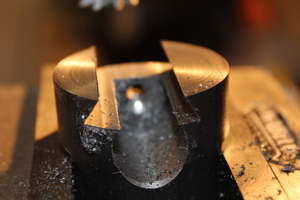
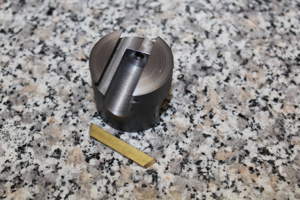
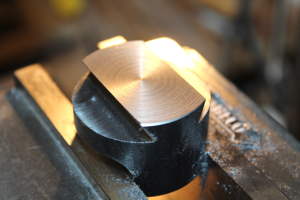
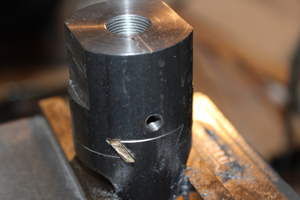
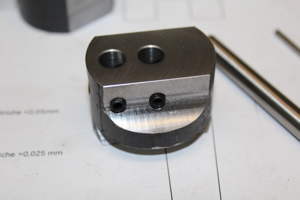
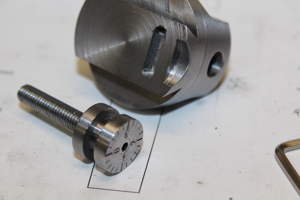
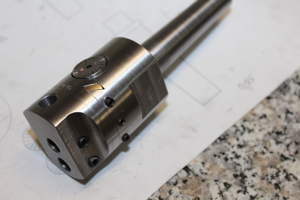
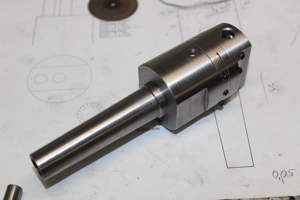
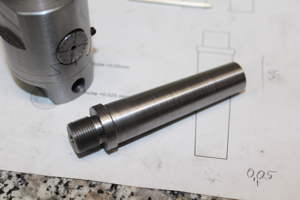
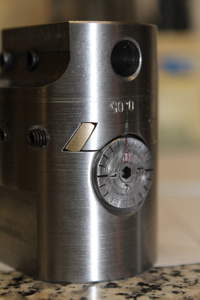
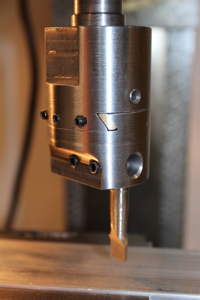
Downloads:
Zeichnung kommt wenn mal Zeit ist... Für Fragen stehe ich aber gerne zur Verfügung.Für die Funktion und Eignung für die eigenen Ansprüche kann ich trotz sorgfältiger Prüfung keine Gewährleistung übernehmen. Nachbau und Nutzung also auf eigenes Risiko!